Daily and weekly routines for department heads
What is a Labor cockpit?
The Labor cockpit is where department heads manage their staff schedules. There is a Labor cockpit for each department in PMI and a department head has been assigned to each one. Here, they manage the staff schedules according to the needs and activity in their department.
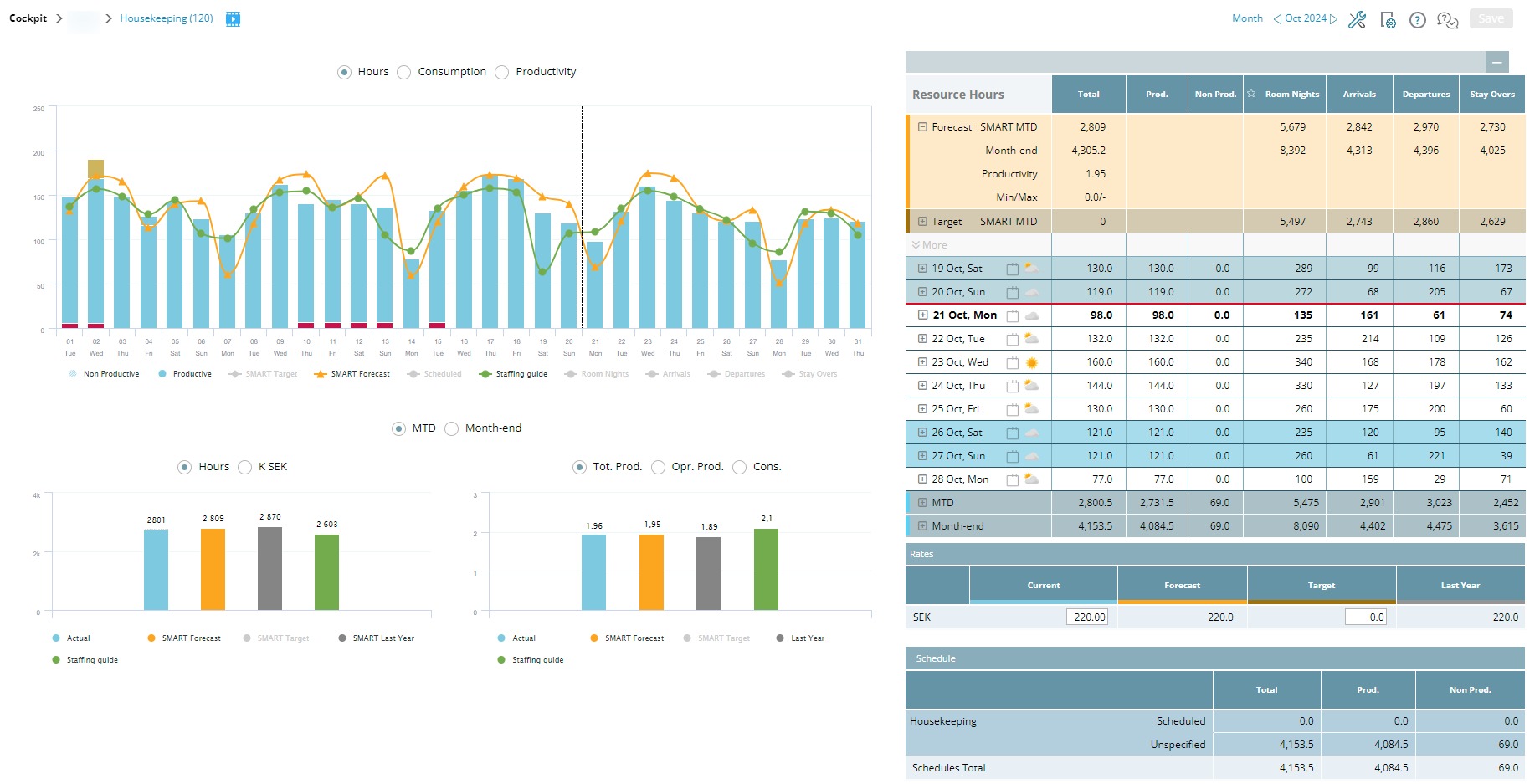
As a department head, your main goals when using the department’s cockpit are to:
- Align your schedule as closely as possible with the daily SMART forecast.
- Monitor productivity:> Ensure your team meets its productivity targets. If they fall short, identify and implement improvements in their workflow.
- Adhere to your month-end SMART hours by tracking month-to-date hours and maintaining alignment with the SMART forecast.
Doing these well helps you achieve a strong score in the Do section of the PMI adoption index.
Recommended Routines:
We suggest monthly, weekly, and daily routines for working with the Cockpit. Completing these consistently keeps data accurate, allowing you to adjust future schedules optimally. This ensures you always have enough staff to handle the workload without overstaffing.
Types of Labor Cockpits:
- Fluctuating Hours Cockpits: Hours vary based on business demand.
- Fixed Hours Cockpits: Hours remain the same each week, regardless of business activity levels.
Labor cockpits with fluctuating business demand
These types of Cockpits include:
- Housekeeping
- Front office
- Restaurants
- Bars
- Breakfast
- Kitchen
- Stewarding
- F&B service
- M&E
- Public area cleaning
Daily Routines (Monday–Friday)
Review
- Verify your previous day’s productive and non-productive hours (blue bars in the graph) are correct. If not, adjust them in your TKS (not in PMI).
- If you use PMI’s scheduling module, apply any necessary edits in the Cockpit for past dates or update the schedule for upcoming days.
- If you used significantly more or fewer hours than forecast or if anything noteworthy happened (e.g., staff sick leave, staff training), add a comment. These comments are visible to management.
Adjust
- Check that your scheduled hours for the upcoming week align with the daily SMART forecast. Make any required changes in your timekeeping system.
- Avoid exceeding your SMART hours month-to-date or month-end without proper approval.
Save
- Click Save once you have finished.
Weekly routines:
- Align: Once a week, align the schedule for the next 2 – 4 weeks in your timekeeping system to the recommended number of hours in PMI and add a new week to your rolling 6-week schedule. Adjust in the timekeeping system as needed.
- If you are working with the scheduling module in PMI, make any changes in the cockpit for the past, or update the schedule for the future.
Discuss with your GM on a weekly basis:
- How well are your team’s schedules aligned to the daily SMART forecast and following business demand?
- Is your team reaching their forecasted productivity target?
- Is your department within your SMART forecast hours month to date and month end?
Monthly routines:
- Review last months results. Did you meet the productivity/hours forecast? Were there any major discrepancies from the SMART forecast? Consider why that may have been.
- Aim for improvement over last month/last year. This requires looking at the routines and finding new and smarter ways to be more productive and reach the targets.
- Look ahead to next month. Are there any changes needed in the forecast? If yes, updates should be made in Budget & forecast module. If you aren’t sure what a realistic forecast looks like, look at the same month last year, and use that as a starting point. The Staffing guide is also helpful to figure out a realistic forecast.
Labor cockpits with fixed hours
These types of Cockpits include:
The routines for Cockpits with fixed hours are similar to those with fluctuating business demand, with a few differences.
Daily routines
- Review: Ensure your previous days’ productive and non-productive hours (blue bars in the graph) are correct. Adjust in the timekeeping system if needed.
- Adjust: Add a comment If something noteworthy happened or you used significantly more or less hours than forecast. E.g., staff are on sick leave and you had to bring in replacements, there was staff training, etc. Comments will also be visible to management from the Management Perspective.
- Save: Once you have verified the hours are correct, click Save.
Weekly routines:
- Align: Once a week, align the schedule for the next 2 – 4 weeks in your timekeeping system to the recommended number of hours in PMI and add a new week to your rolling 6-week schedule. Adjust in the timekeeping system as needed.
Monthly routines:
- Review last months results.
- Look ahead to next month. Are there any changes needed in the forecast? If yes, updates should be made in Budget & forecast module.
Sticking to these routines will improve your hotel’s GOP and ensure a consistent standard of guest service.
See this article for more details on a Labor cockpit.
Troubleshooting tips
This section provides additional troubleshooting advice for readers experiencing specific issues. While it’s packed with useful insights, you may skip it if you’re not facing any related problems.
Why is there a big difference in SMART hours between two months?
If you notice a significant difference in SMART hours between two months — like April and May — the most common explanation is a change in the Productivity forecast.
Quick Explanation
SMART hours are calculated using the following formula:
SMART Hours = Cost Driver ÷ Productivity Forecast
So, if the Productivity forecast is lower in May, even with the same cost driver (like number of covers or revenue), the result will be higher SMART hours. This doesn’t necessarily mean your staffing increased — it reflects a lower productivity expectation for that period.
What To Check
- Compare the Productivity forecast for both April and May.
- Look at the Cost Driver (e.g., revenue, covers) to see if it stayed consistent.
- Confirm that Productivity is set as the selected forecast in your SMART setup.
By aligning the forecast expectations with actual performance, you’ll get clearer insight into staffing efficiency across periods.
Why is the hours total different in the table and the graph?
The difference in hours comes down to the type of forecast being displayed:
- Management Forecast (Table): This is the forecast set manually by management, based on their expectations and strategic goals. It reflects planned hours to meet operational needs.
- SMART Forecast (Yellow Bar in Graph): Generated by PMI’s SMART system, this forecast uses machine learning and historical data to provide a dynamic suggestion. It factors in monthly productivity goals and current hotel activity.
The variation between these two forecasts highlights the difference between static planning (Management Forecast) and data-driven predictions (SMART Forecast). Use this insight to adjust plans as needed for better alignment with real-time performance and goals.
Why can’t I see the “ Add Note ” icon in a department’s Schedule table?
Symptom
In one cockpit the Schedule table shows no note icon beside the daily hours, while other departments do show it.
Cause
That cockpit contains more than one schedule row for the same day (e.g., “Front Office – Scheduled” + “Reservation desk”).
When several rows exist, PMI collapses them into a single line. The note icon only appears once you expand the day so PMI knows which row you want to annotate.
Quick fix
- In the Schedule table, click the plus symbol to expand the date.
- Each underlying schedule row now displays its own note icon.
- Click the icon, type your note, Save, and collapse the day again if you like.
Tip
If you often use notes, keep the days expanded while you’re adding comments, then collapse them for a cleaner view.
Why can’t I edit rates for a past month?
Issue: You’re trying to change rates (or other values like hours, productivity, or labor costs) for a past month in PMI—like April—but the fields are locked and uneditable.
Why It Happens
PMI automatically locks all historical data to preserve reporting accuracy. Once a month ends, the system treats that data as actuals, not forecasts. This affects all modules, including the Cockpit and Budget & Forecast.
What to Do
You’ll need to unlock the period using Period locking:
- Go to Advanced settings → Period locking
- Find the padlock icon for the relevant month (e.g., April)
- Click it to unlock the period
Once unlocked, all related values for that period become editable across the system.
Important Notes
- Only users with elevated rights (like Admins or Revenue managers) can unlock past periods
- If you don’t have access, contact your PMI administrator
- Treat unlocked periods with care—editing actuals should always be intentional and documented
Why are my SMART hours a straight line?
If your SMART forecast displays a flat line—such as 3 hours per day—it typically indicates that the system is constrained by specific settings, preventing dynamic adjustments based on activity levels.
Primary Cause: Min/Max Settings
The most common reason for this issue is that the minimum and maximum hours in the SMART configuration are set to the same value. This setup restricts SMART from adjusting hours in response to fluctuations in demand or activity.
How to Check and Adjust Min/Max Settings
- Navigate to the Cockpit:
- Open the relevant department’s Cockpit in PMI.
- Access Tools and Settings:
- Click on the Tools and Settings icon (usually represented by a gear or wrench symbol).
- Review Min/Max Hours:
- Locate the Min/Max Hours section.
- Check if the Minimum and Maximum hours are set to the same value (e.g., both at 3 hours).
- Adjust Values:
- If both values are identical, modify them to allow flexibility. For example:
- Set Minimum Hours to 2.
- Set Maximum Hours to 5.
- This range enables SMART to allocate hours dynamically based on actual demand.
- Save Changes:
- After adjusting, ensure you save the changes to apply the new settings.
Additional Considerations
- User Permissions: Ensure you have the necessary permissions to modify Min/Max settings. If not, contact your system administrator.
- Historical Data: If SMART lacks sufficient historical data, it may default to static values. In such cases, consider manually adjusting the forecast or consulting with your administrator.
- Cost Driver Accuracy: Verify that your primary cost drivers are accurately forecasted. Inaccurate inputs can affect SMART’s calculations.
What happens when forecasts remain at Staffing-guide defaults?
If a department’s forecast isn’t updated and remains at the staffing-guide default beyond the expected deadline, the PMI Adoption Index will indeed display this as a hygiene factor. These hygiene factors are marked in red to draw attention and indicate areas requiring action to maintain data integrity and operational efficiency. However, hygiene factors generally do not directly impact the index score, except for those related to Rooms management, which do affect the score due to their impact on forecasting accurac
Best Practices to Address This:
- Regularly Review the PMI Adoption Index: Monitor for any red-marked hygiene factors indicating unupdated forecasts. 
- Update Forecasts Promptly: Ensure that departmental forecasts are reviewed and updated regularly to reflect current expectations and avoid reliance on default staffing-guide values.
- Utilize the Staffing Guide Effectively: While the staffing guide provides baseline recommendations, it’s essential to adjust forecasts based on real-time data and departmental insights.
By proactively managing forecasts and addressing hygiene factors, departments can ensure accurate staffing levels and maintain optimal operational performance.
Understanding the Scheduled Horizon and Graph Lines
The Scheduled Horizon in PMI shows how far into the future schedules are active and where PMI’s SMART forecast begins.
In Legacy Tables and Schedule Views:
- Red vertical line = Today
- Dashed green vertical line = Scheduled Horizon
- Beyond the green line, users can manually enter schedules. If left blank, PMI auto-generates SMART hours.
In the Day-to-Day (Labor Graph) View:
- Dotted black vertical line = Today
- Dashed green vertical line = Scheduled Horizon
These visual markers help you compare scheduled hours with PMI’s suggested SMART schedule.
If you don’t see the Scheduled Horizon or Today lines:
- You may not be in the graph (Day-to-Day) view
- You may be viewing past or already finalized periods
- Your user role or cockpit view setup may limit what’s shown
Tip: The Scheduled Horizon is usually set by the Head of Department (HOD) under View Settings — often to a fixed number of days ahead (e.g., 14, 28 or 90). If you don’t see the green line immediately, try using the date picker to advance one month at a time — the Scheduled Horizon may be set further into the future.
Scheduled Horizon Misunderstanding
The Scheduled Horizon setting often leads to confusion. Adjusting it does not affect the import of hours from your Timekeeping System (TKS). It only determines how far into the future you can view data. If you’re missing data, the issue likely lies with TKS data or mapping settings, not the Scheduled Horizon. There are visual differences in the appearance of the Today and Scheduled Horizon lines, as described below:
Cockpit View:
- Day-to-day graph:
- Black dotted vertical line: represents today’s date (Today Line).
- Green dashed vertical line: marks the end of the Scheduled Horizon.
- Cockpit Table:
- Horizontal red line: indicates today.
- Horizontal green line: shows the end of the Scheduled Horizon.
Schedule View:
- Vertical red line: represents today’s date (Today Line).
- Vertical green dashed line: shows the end of the Scheduled Horizon.
Links:
Providing context for better insights
Issue: Users ask broad questions like “Where is my data?” or “What do these figures tell you about my productivity?”without providing sufficient context or visual input.
If you're unsure why specific data or insights aren't displaying as expected, ensure your query includes enough context. You can also use the Query Library, which offers premade queries tailored to common needs—screenshots are automatically added when required for these queries.
For custom queries, consider taking a screenshot of the relevant data or view by clicking the camera icon. Providing clear context or visuals helps the AI analyze your data more effectively and deliver accurate responses.
Productivity based hours
These are typically used for operational departments where productivity is the main target. When the cost driver (e.g., room nights, revenue) changes, PMI automatically recalculates the required hours to maintain the fixed productivity target. This keeps your labor plan aligned with real activity levels.
What to do:
- Go to PMI cockpit → Select your department
- Click the gear icon to access settings
- Under the Forecast settings, ensure the “Productivity is locked” option is enabled
- Save changes to apply productivity-based forecasting
For example, if more rooms need cleaning next month, the Housekeeping department will automatically receive more hours to meet the productivity target (e.g., 0.25 HRS/RN).
Modifying “Other hours” via Data upload center
Yes, "Other Hours" can be modified using the Data upload center in PMI. However, understanding the difference between "Other hours" and "TKS hours" is crucial:
- TKS Hours: These are hours imported directly from your external Timekeeping System (TKS). They represent scheduled or actual hours recorded externally and synced with PMI. These hours cannot be edited directly in PMI.
- Other Hours: These are manually added hours or hours not imported via TKS, such as outsourced labor or specific tasks. These can be adjusted directly in PMI, including through the Data Upload Center.
Steps to Modify "Other Hours"
- Go to the Data Upload Center in PMI.
- Select the appropriate template for labor data upload.
- Input the correct department, date, and "Other Hours" values.
- Upload the file and verify changes in the Labor Cockpit.
For more details, refer to the Daily Routines in Labor Cockpit guide.
Low SMART Hours?
If your cockpit displays unexpectedly low SMART hours, the most common cause is that the Productivity forecast is set too high.
Why This Happens:
- The SMART forecast is calculated by dividing the primary cost driver forecast by the Productivity forecast. When the Productivity forecast is inflated, the resulting SMART hours decrease.
What to Do:
- Review the Productivity Forecast: Check that the forecast value accurately reflects realistic performance targets.
- Adjust and Recalculate: Modify the forecast if necessary and recalculate the SMART hours to see the updated totals.
For more detailed steps, refer to our SMART cockpit guide.
Key Notes for Adjusting Min/Max Settings
- Effect of Changes: Changes to Min/Max settings will impact the current year and all future years but will not apply to past years.
- Global Application: Adjustments to Min/Max hours are applied globally to the selected year, not on a month-by-month basis. Always ensure the correct year is selected before making changes.
Incorrect codes in TKS
Make sure the correct codes have been used in your TKS. If the hours are still not correct after the next import, there may be an error in the mapping – please contact your controller who will make the necessary changes.
Inability to edit data for a specific period
A "frozen" screen issue could be related to period locking. This would result in an inability to make any modifications to schedules, reports, or other entries for a specific period.
- Check the Period Locking Settings: This issue is often related to the period locking feature in the PMI system. When a period is locked, it prevents any changes from being made for that time frame. Check the period locking settings for the specific month to see if it has been mistakenly set to close.
- Unlock the Period: If the period for the specific month is locked, you will need to unlock it. This can be done by accessing the period locking settings in the PMI system. Double click on the padlock icon for the specific month to unlock the period. Note that you may need administrative rights to do this.
- Contact PMI Support: If the issue persists even after unlocking the period, or if you are unable to unlock the period due to lack of permissions, contact the PMI support team for further assistance.
I can’t enter the closing value for food inventory
In PMI, the Closing inventory value for one month automatically becomes the Opening inventory value for the following month. If the field appears locked or non-editable, here’s what to check:
Possible Reasons & What to Do:
1. The period is locked
- Once a month has ended, PMI treats it as finalized (actuals). Fields like Closing inventory are locked to protect reporting accuracy.
- Solution: Ask your administrator to unlock the period using Period locking (found under Advanced Settings). Once unlocked, you’ll be able to enter or adjust the value.
2. You don’t have editing rights
- While most F&B Managers or Controllers do have access, some user roles might be restricted from editing actuals.
- Solution: If you’re unable to edit even after the period is unlocked, contact your local admin or support team for assistance.
Tip: Always save after making edits, and verify that the Opening inventory for the next month reflects your updated value.
How to compare TKS hours with hours in PMI
To compare actual worked hours from your Timekeeping System (TKS) with the scheduled/planned hours in PMI, use the Labor Cockpit:
Steps to Check:
- Go to the Labor Cockpit
- Select the relevant department and date range
- Click the plus sign next to the date to expand the daily detail
- You’ll see:
- Scheduled hours (what was planned)
- TKS hours (what was actually worked and imported from your Timekeeping System)
- Hours broken down by productive and non-productive categories
You can also hover over bars in the graph to compare day-by-day totals visually.
Tip:
- If the numbers don’t match, check whether:
- The TKS import has been processed for the current period
- The department and role mappings between TKS and PMI are up to date
- Any manual adjustments were made in TKS or PMI after the import
How to check if schedules match the demand forecast
To make sure your schedules reflect the current demand, do a quick visual check in the Labor Cockpit:
What to Look For:
- Blue bars: Represent scheduled hours.
- Yellow line: Indicates the SMART Forecast, which is system-generated based on targets and cost drivers.
- Green dashed line: Marks the Scheduled Horizon, showing how far ahead scheduling is active
Your scheduled hours (blue bars) should closely follow the yellow SMART Forecast line. If they’re significantly above or below, it may indicate over- or under-scheduling.
Where to Check:
- Go to the Labor Cockpit
- Select the correct department and date range
- Compare the visual graph — especially just beyond the green dashed line
Tip: If the SMART Forecast seems off, click the forecast icon to review the SMART and Management Forecast values.
How does PMI handle departments with zero historical data when calculating SMART-schedule guidance
If a department has no historical data, PMI cannot use its SMART algorithms, which rely on past patterns to suggest efficient staffing levels.
Instead, PMI falls back on cost driver logic as the primary basis for scheduling guidance:
Here’s how it works:
- Cost Driver-Based Scheduling: The system uses a linked cost driver (e.g., room nights, covers, revenue) to estimate required hours. This provides a baseline forecast tied to expected business volume.
- Default Productivity Values: PMI may apply default productivity ratios (e.g., hours per 100 room nights) if defined in the configuration or mappings.
- Manual Inputs & Adjustments: Users can manually enter forecasted hours based on expected needs, and these can later be refined as actual data becomes available.
- No ML or Smart Hours Yet: Since Smart-schedule guidance depends on past performance trends, departments with no prior year’s hours won’t benefit from it until a baseline has been established.
Tip: If you’re setting up SMART for a new department, ensure a cost driver is assigned and mapped. This allows the system to provide at least basic forecasting support until historical data builds up.
Adjusting decimal precision in the labor cockpit table
If you're having trouble manually entering decimal precision in the cockpit table, please review the settings in the Tools menu:
- Open Tools Menu: In the PMI Labor Cockpit, navigate to the Tools menu 1 .
- Access Settings: Click on "Settings" within the Tools menu 1 .
- Change Decimal Precision: Find the option for setting the number of decimals for hours. Adjust to your preference.
- Save Changes: Confirm and save your changes.
- Check Changes: Return to the Labor Cockpit to ensure your changes have been applied correctly.
If the issues persist, consider reaching out to PMI support for further assistance.